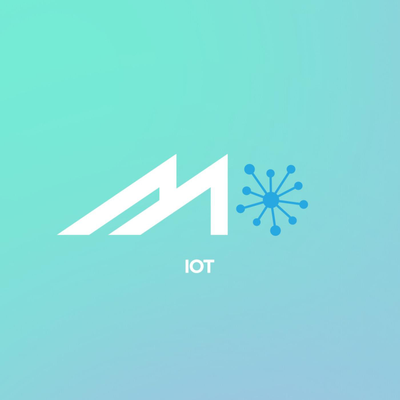
Industrial IoT by MarketScale
Podcast af MarketScale
Prøv gratis i 7 dage
99,00 kr. / måned efter prøveperiode.Ingen binding.
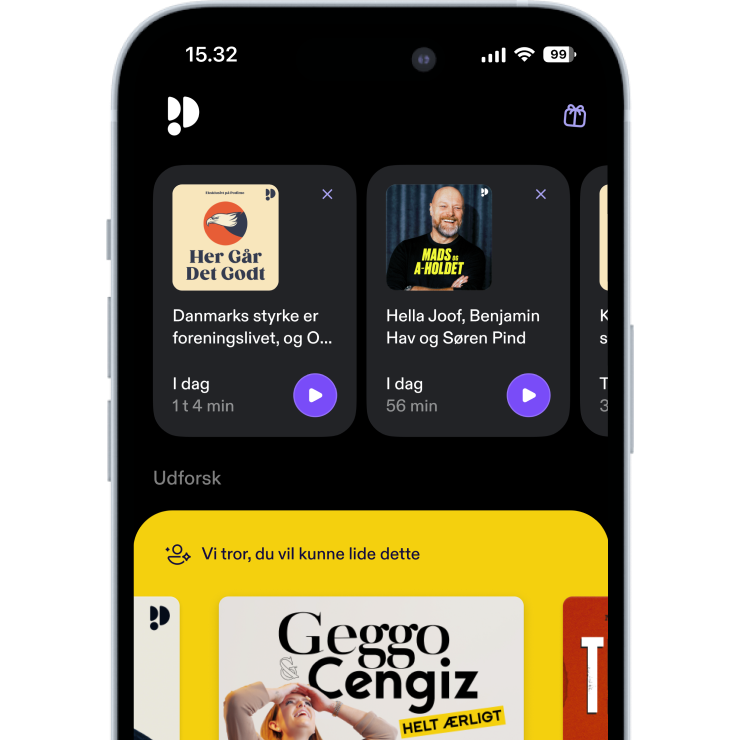
Mere end 1 million lyttere
Du vil elske Podimo, og du er ikke alene
Rated 4.7 in the App Store
Læs mere Industrial IoT by MarketScale
Welcome to the Industrial IoT podcast, by MarketScale: Your home for everything B2B in the Industrial IoT world. Join us for new episodes every week featuring conversations with industry leaders as we explore trends in technology, use-cases & applications, hurdles, and all things IoT.
Alle episoder
67 episoder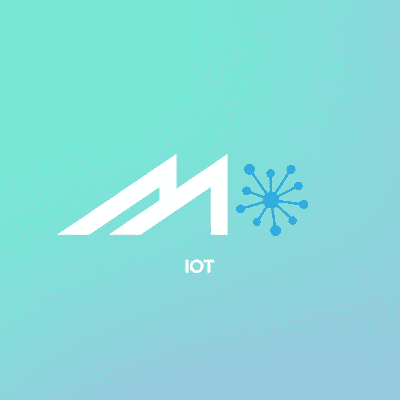
On this episode of the Industrial IoT Podcast, http://marketscale.com/industries/contributors/adam-livesay/, co-founder, and CEO at https://www.elevat-iot.com/, joined host Geoffrey Short to discuss how businesses and industries are blending this technology into their machines and getting value out of it. Elevāt.IoT specializes in connecting fleets of machines and enabling the flow of data between operators, distributors, and OEMs since 2015. How can business owners and decision-makers use this technology to better improve their workflows? Livesay said businesses first need a strategy on what problem they are trying to solve. Once they know that, they need to put an IoT team into place. Livesay said businesses are recognizing the ROI from IoT. There’s an evolution of comprehension since 2015 around what IoT can accomplish and the ROI it can bring to a business. “Deployment,” Livesay said, “has gone down from 18 months for a successful production deployment, to less than six months.” Short asked Livesay how Elevāt.IoT has utilized this technology. Livesay provided an example of working with nut companies to put IoT on their tree shakers to generate significant process improvement data never before available to them. Livesay sees a great opportunity in collaboration of information share throughout the whole ecosystem of industrial machines as the evolution of IoT. With the costs of deploying IoT going down tremendously over the past few years, now is a great time for businesses to explore their IoT strategy.
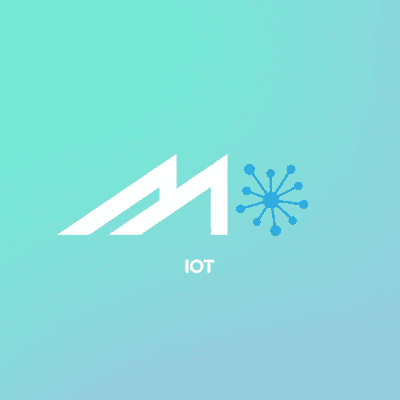
The business world relies on data; there's no escaping it, and there shouldn't be a desire to. Sophisticated data analysis is making business more efficient across the board. On this episode of the MarketScale Industrial IoT Podcast, http://marketscale.com/industries/contributors/lane-leach/, Senior Systems Engineer for https://www.pbsnow.com/, sat down with host http://marketscale.com/industries/contributors/sean-heath/ and they discussed the complex challenge of backing up a company’s critical systems. The most reliable way to recover from a catastrophic data corruption event is to restore the necessary systems from their backups. As Leach points out, for many companies, those backups simply were not created, whether through oversight or lack of priority. “It doesn’t take more than a few minutes of having that be unavailable to be a quick reminder of how important it really is," he said. The stark impact of not having a comprehensive backup plan is clearly reinforced during a crisis, according to Leach. “It could cripple your business to the point where you may have to go out of business,” he said. Leach explained that not all dangers are unforeseen. He described a situation occurring in California to illustrate the need to prepare for expected issues, as well. “Because of fires, you have the major electrical utility provider making a proactive decision, in their case, to have power outages. Well, imagine your business being in one of those impacted and affected counties and not having power for several days,” he said. “Where is your data? Is that something your business can withstand?” The majority of businesses focus on the wrong side of the data backup equation, offered Leach. “If we approach high availability and business continuity from a perspective of the data, and not the equipment, let’s start there,” he suggested. “The place to start is: what can I live without?”
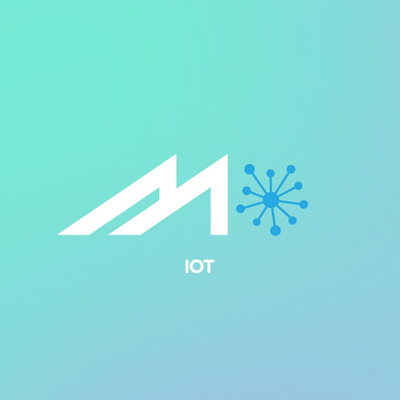
Manufacturing companies can often be slow to adopt new technology. It’s not because they have doubts about the potential; it’s typically because of the disruption of implementation. This especially true when it comes to finishing systems. Manufacturers may feel literally “chained” to the traditional chain systems. Today, we’re joined by http://marketscale.com/industries/contributors/john-claman/, Sales Rep and Marketing Supervisor of https://www.intellifinishing.com/ to talk about what opportunities manufacturers have with alternatives to chain systems. John said, “At some point, manufacturers will begin to see the need to upgrade their finishing systems for better quality and better throughput. This creates the need for automation and new technology. But it doesn’t come without challenges.” The monorail system for parts finishing goes back to the days of Henry Ford and is still used in many settings. The problem with these chain conveyors is that they are very limited. They only go in one direction and at a certain speed. There’s really no way to customize, leaving manufacturers often unable to innovate. John shared, “With a monorail system, you are locked into one speed. So, let’s say a new paint becomes available that has a shorter cure time. It would be hard for a business to use the new paint because they don’t have any control over timing.” IntelliFinishing has rewritten the book on manufacturing painting systems with their friction tube system. It doesn’t use chains but rather has aluminum tubes connected to trolleys. It offers much more flexibility. “No chains mean you can scale and change the conveyor system based on your needs. And one of the greatest benefits of the system are that it can greatly reduce energy costs associated with idle equipment and heat loss,” John said The difference in the friction tube system is that it can move forward and backward as well as have adjustable timers. Further, the way that ovens are used for curing is improved because the whole system doesn’t go in the oven, just the product. “We recently assessed a system for a customer and found that our system could reduce heat loss by 18%,” John commented. Find out more about the IntelliFinishing system and how it’s changing manufacturing painting processes by listening to the podcast.
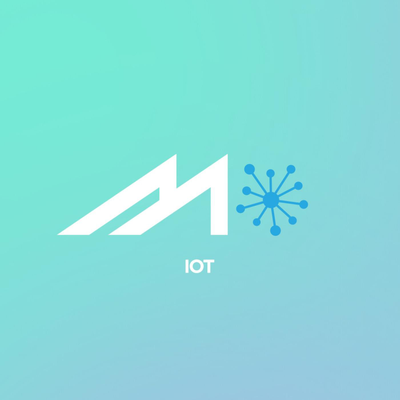
Computerized maintenance management software is arguably one of the important purchases you'll make in manufacturing, but as our guest today on the podcast can tell you, it's a complicated process. In this new episode, host Sean Heath sat down with http://marketscale.com/industries/contributors/steve-reed/, Vice President of Safety and Engineering at https://www.kasacontrols.com/, for answers to all your CMMMS questions. So, how do you know you're using all the functions efficiently, if at all, and what do you do when it comes to integrating that CMMMS with your control system? Those are issues that companies often face when implementing new software or technology, Steve said. "Like a lot of software packages, people get accustomed to using certain features within them but there are other capabilities within those tools that they don't necessarily use," he said, explaining that initial training at installation doesn't necessarily mean your team is using all possible functions correctly. He suggests going back through the features with the manufacturer every few years to ensure all features are being utilized and new team members are receiving firsthand training. Also in this episode, Steve discussed how industrial IoT can aid predictive maintenance scheduling in a meaningful way. "If you do your predictive maintenance accurately and reliably by integrating the control system into your CMM, you can easily predict these imminent failures well in advance," Steve said. "You can manage that in a smart way before it's an emergency."
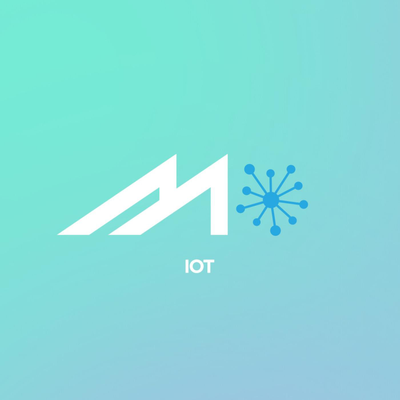
The Internet of Things has allowed people to be more efficient in their routines for years, and businesses are increasingly implementing the technology into their own. Industrial conglomerate Honeywell announced it is adding more automation, cybersecurity and visualization tools to its ‘Forge for Buildings’ IoT platform. Honeywell CEO Darius Adamczyk told CNBC the company is also investing in robotics, amongst other smart tech. Another American institution, Kentucky Fried Chicken, is also implementing the latest innovations in its field. At least for now. The company began testing plant-based chicken yesterday through a partnership with Beyond Meat. The meatless nuggets and wings are available at just one KFC location in Atlanta right now, but if tests go well, the new menu item could be at a location near you soon. Yahoo Finance reports that the product contains about 20 ingredients, with its core component being a pea protein. Tune in to Business Casual, MarketScale’s live radio broadcast, every Wednesday and Friday at 8 a.m. CST.
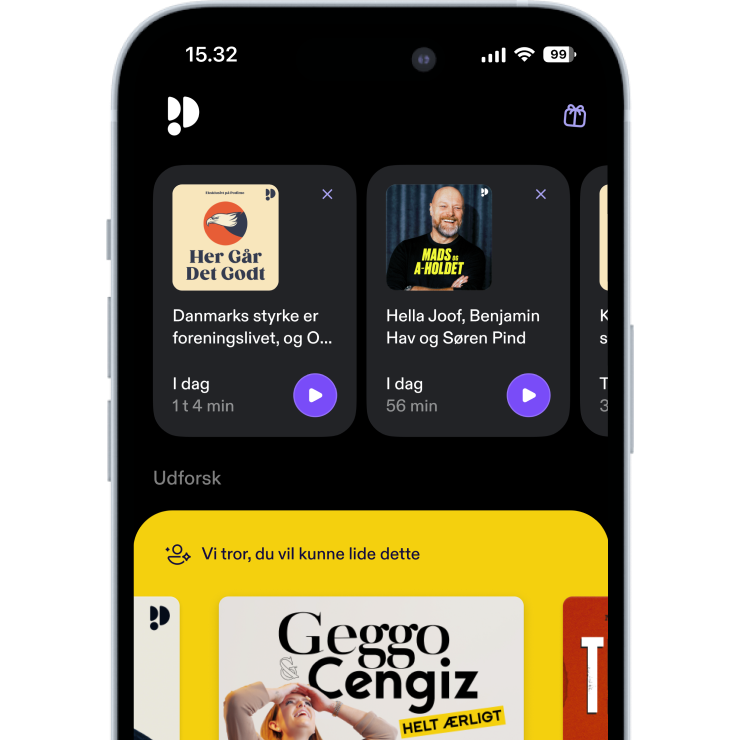
Rated 4.7 in the App Store
Prøv gratis i 7 dage
99,00 kr. / måned efter prøveperiode.Ingen binding.
Eksklusive podcasts
Uden reklamer
Gratis podcasts
Lydbøger
20 timer / måned