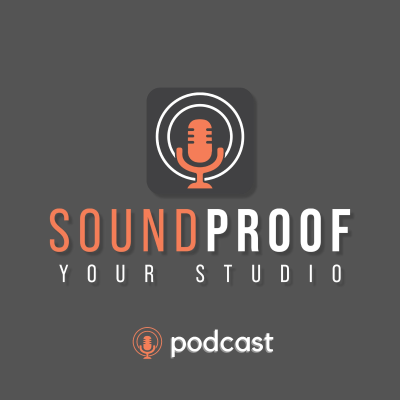
Soundproof Your Studio
Podcast af Wilson Harwood
Prøv gratis i 7 dage
99 kr. / måned efter prøveperiode.Ingen binding.
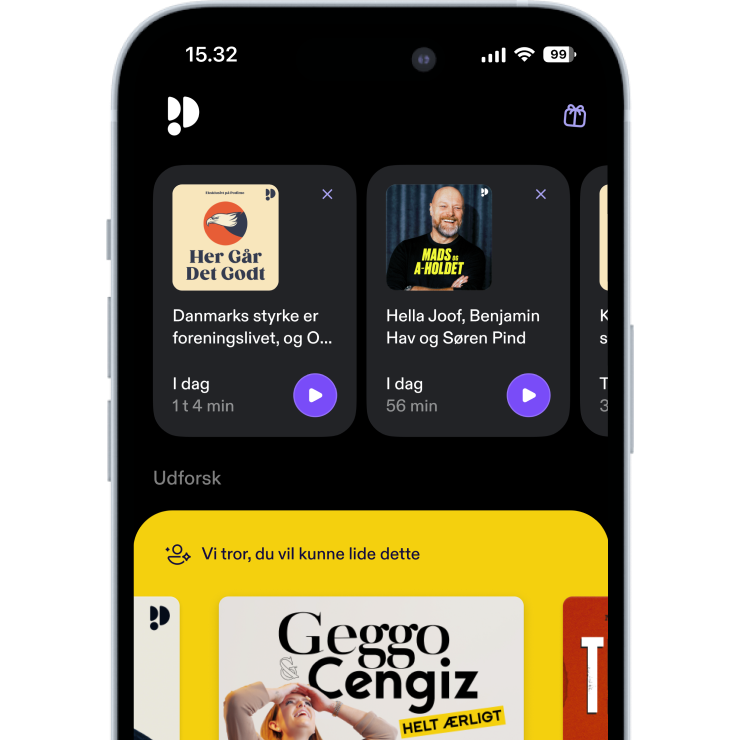
Mere end 1 million lyttere
Du vil elske Podimo, og du er ikke alene
Rated 4.7 in the App Store
Læs mere Soundproof Your Studio
I teach you how to build a soundproof studio. Even if you know nothing about soundproofing or construction I go in depth to turn you from a total beginner into a soundproofing master.
Alle episoder
173 episoder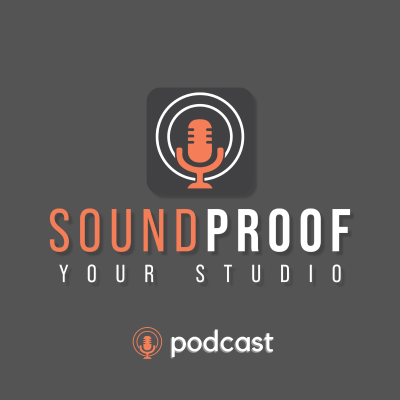
📅 Book Your Free Call: https://www.soundproofyourstudio.com/Step1 [https://www.soundproofyourstudio.com/Step1] FREE Soundproofing Workshop: https://www.soundproofyourstudio.com/workshop [https://www.soundproofyourstudio.com/workshop] How to Build a Pro Recording Studio in Your Backyard– Part 2: HVAC & Acoustics That Actually Work So, you’ve got a dream of laying down Grammy-worthy tracks right in your own backyard. 🎶 In Part 1, we tackled the big stuff, framing, wiring, walls, and ceilings, the bones of your studio. Now in Part 2, we're getting into the quiet heroes of pro studio design: your HVAC system and acoustic treatment. 🛠️🎧 These may not sound glamorous, but trust me, they’re game-changers. WHY HVAC ISN’T BORING (ESPECIALLY IN A STUDIO) Imagine you’re in the middle of a fire take with a full band. It’s hot, the room’s stuffy, and now your guitar’s out of tune because of humidity. Not the vibe. That’s why I designed an HVAC setup built to handle up to 15 people in one studio, without overheating you or your recordings. It’s not just about airflow, it’s about quiet, efficient air movement that doesn’t mess with your mix. Here's what makes it work: ✅ Broan ERV (B210 E75RT) – Brings in 210 CFM of fresh air while keeping outside noise out. 💧 Aprilaire E-100D Dehumidifier – Keeps the humidity in check so your gear and vocals stay happy. 🔄 Separate duct loops for the ERV and dehumidifier = ultra-quiet performance. Bonus: I color-code all the ducts for clarity. 🔴 Red = Return Air 🟢 Green = Supply Air Simple. Clean. Effective. BAFFLE BOXES = HVAC THAT DOESN’T RUIN YOUR TAKES Baffle boxes are one of those “hidden gems” most people overlook. But they’re critical if you want your HVAC system to stay silent during takes. Here’s how I do it: * Mounted with neoprene rubber to stop vibration in its tracks * Lined with 1" acoustic duct board to kill airflow noise * Every seam is sealed like your studio depends on it, because it does Paired with a chimney-style duct design, this setup keeps the air moving and the noise out. MINI-SPLITS: PERSONAL CLIMATE CONTROL, NO COMPROMISE Each room, live and control, gets its own mini-split unit, so you can dial in the perfect temp for each space. No shared vents, no sound bleed. Pro tip: Install them before drywall goes up. It'll save you money (and a headache) later. ACOUSTIC TREATMENT THAT’S ACTUALLY DESIGNED, NOT DUCT-TAPED TOGETHER Forget those random foam squares stuck on the wall. This is intentional, engineered, and easy-to-follow acoustic treatment, that also looks damn good. I teamed up with GIK Acoustics for a treatment plan that includes: 🎯 Bass traps in all four corners — bye, boomy low-end 🌀 Diffusers to tame reflections and harshness 📦 Labeled panels with a full materials list so you know exactly what to install, and where And yes, you get 3D renderings of your studio layout, so both you and your contractor are on the same page. THINKING DIY? YOU’VE GOT THIS. I know, building a studio like this sounds intense. But with the right plan, clear visuals, and a solid system, you can 100% pull this off, even as a DIYer. To help you out, I offer: 🛠️ A free soundproofing workshop [https://www.soundproofyourstudio.com/workshop] 📞 A free clarity call [https://www.soundproofyourstudio.com/Step1] to talk through your build 📋 Complete materials lists and system diagrams to keep your project moving smoothly Whether you’re doing it yourself or bringing in help, this part of the series is your go-to guide for HVAC and acoustics that actually work.
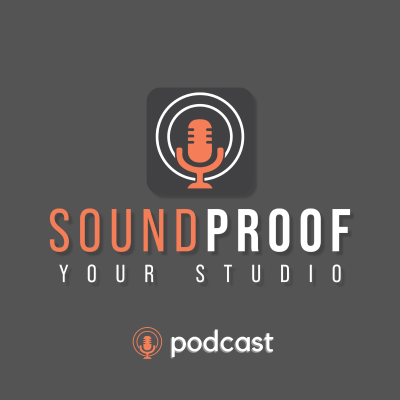
📅 Book Your Free Call: https://www.soundproofyourstudio.com/Step1 FREE Soundproofing Workshop: https://www.soundproofyourstudio.com/workshop [https://www.soundproofyourstudio.com/workshop] 🛠️ HOW TO BUILD A PROFESSIONAL RECORDING STUDIO IN YOUR BACKYARD So, you're ready to turn your backyard into a chart-topping, soundproof masterpiece. A place where genius flows, beats drop, and neighbors don’t complain. Whether you're a drummer, podcaster, producer, or just want a reason to escape your family for "work", this guide’s for you. Grab your hard hat (and your dreams), and let’s build a recording studio that actually sounds good. 🎧 STEP 1: DREAM BIG, DESIGN SMART Let’s kick things off with a design that slaps. We’re talking about the ultimate combo: * Control Room 🎛️ * Live Room 🥁 * Kitchenette ☕ And yes, even a Bathroom 🚽 (because inspiration strikes at weird times). Sound quality doesn’t come from wishful thinking, it comes from high-quality design. Your studio should be a sanctuary for clean sound, not a glorified garden shed. 🧠 STEP 2: FREE RESOURCES YOU’D BE SILLY NOT TO USE Before you sketch your first wall or glue your first acoustic panel, visit: soundproofyourstudio.com/workshop [https://www.soundproofyourstudio.com/workshop] This free workshop is basically a cheat code for building studios. Trust us, future you and your bank account will thank you. 📐 STEP 3: IT’S FLOOR PLAN TIME, BABY Start with the A1.1 sound isolation plan. Sounds fancy because it is. Your floor plan should include: * Control Room (aka your audio command center) * Live Room (aka the vibe factory) * Kitchen Entryway (snack-friendly) * Bathroom (self-explanatory) Pro tip: Throw in diagrams for windows, doors, and acoustic panels. These little details make a big difference. 🏠 STEP 4: RAISE THE ROOF (LITERALLY) Your control room? Lifted ceiling. Your live room? Flat ceiling. Your humidity? Controlled (thanks, dehumidifier). Also, layer your roof with OSB + EPS materials for that sweet, soundproof silence. Science never sounded so good. 🔥 STEP 5: FIRE STOPS – BECAUSE SAFETY IS SEXY No one wants a studio that’s fire. Like, actual fire. Double wall systems need proper fire stops. Use: Drywall Acoustic decoupling clips That way, your studio stays safe and silent. 📏 STEP 6: SECTION IT OFF Get into the nitty-gritty with building sections. We're talking: Control room + kitchen entryway dimensions Acoustic treatment layering Because precision equals perfection. 🧱 STEP 7: THE WALLS THAT ROCK (BUT DON’T LET SOUND THROUGH) Design wall sections with: Stud spacing (16" or 24" on center) Insulated double wall design Basically, you want walls that hear nothing. Like a secret agent. A very dense, wooden secret agent. 🚪 STEP 8: DOORS & WINDOWS THAT DON'T LEAK SOUND (OR SOUL) Install ISO Store doors with rubber seals tighter than your drummer's schedule. For windows, we recommend Soundproof Windows Inc. They're basically sunglasses for your studio, cool, protective, and no one hears what’s inside. ⚡ STEP 9: LET THERE BE SOUND (NOT BUZZING) Design an electrical plan that avoids the dreaded hum of doom. That means: * Audio-only outlets * Star grounding system * Cable routing that doesn’t look like spaghetti * A quiet studio is a happy studio. 📋 STEP 10: REVIEW LIKE YOUR CAREER DEPENDS ON IT (BECAUSE IT MIGHT) Before swinging a hammer, review the plans. Twice. Then let your team review them again. Not sure if you’re ready? Book a Clarity Call [https://www.soundproofyourstudio.com/Step1]with the experts to double-check everything before the chaos begins. ⚠️ Cautionary Tales from the Soundproof Trenches Always follow your local building codes (no one likes fines). Talk to a structural engineer, especially if your live room is bigger than your kitchen. 🛠️ BONUS TIPS FOR SANITY & SUCCESS Use 3D modeling software like SketchUp to visualize before you build. Keep open communication with your contractor (unless you like redoing things). 🎬 FINAL THOUGHTS: YOUR BACKYARD, YOUR BILLBOARD-READY STUDIO Building a recording studio in your backyard is no small feat, but with the right plan, it can be a game changer. Whether you’re aiming to produce the next Grammy-winning album or just want better acoustics for your podcast intros, this blueprint puts you ahead of the game. So grab your blueprint, fire up that SketchUp model, and let your backyard become the birthplace of your best work.
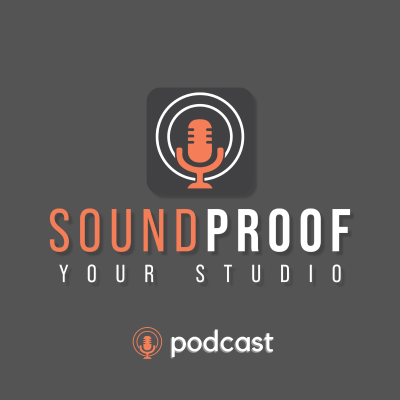
FREE Soundproofing Workshop: https://www.soundproofyourstudio.com/... [https://www.youtube.com/redirect?event=video_description&redir_token=QUFFLUhqbTFSbE1qZDVmMnZxdjBtZnlyN2o4U0N6UkN5d3xBQ3Jtc0tsREk2TG9WQWJyY2I5WTEzWGw5aUVWdDFPb2N6WWhCREp6RnFuckoxY2dIaXBHcWRlenFLLW9RVGIteVp1TXpMM1FpZVVGV3pKbFgtc1RMd0xNNU1Xekc1UW1kZ3plWTV6b2locVNrNUZZX3A3MHM4bw&q=https%3A%2F%2Fwww.soundproofyourstudio.com%2Fworkshop&v=iets8GPXpB8] 📅 Book Your Free Call: https://www.soundproofyourstudio.com/... [https://www.youtube.com/redirect?event=video_description&redir_token=QUFFLUhqbnd4T1kxN1JIQUhNYVFveEktb2pnWmJ3Xy1MZ3xBQ3Jtc0tueVRuWVJJM3RVRHNfaklhdXBEQTRyTmhJNEZ0cG9LbmhSTDNXalFmTG8yRWZPRkQzRks3SG1lRGRxSk9qcHEzamdjc1VGVEJCYmNOOERtb3c4T1ZrZHA0NDVKTldjeWxveGM2R2xsWkplZnJIQV9Xaw&q=https%3A%2F%2Fwww.soundproofyourstudio.com%2FStep1&v=iets8GPXpB8] You’ve got the perfect mic, your preamps are pure magic, and the room’s been acoustically treated to perfection. But then... WHOOOOSH! Your HVAC system sounds like it’s trying to join your band. Not ideal when you're trying to record a delicate vocal track or a whispery acoustic guitar. Welcome to the world of soundproof HVAC design, where the air flows silently, like a ninja in socks. Today, we’re diving deep (but quietly) into one of the most overlooked parts of studio design: air speed. Let’s break it down with some laughs, some math, and some very real solutions (and no, duct tape isn’t one of them). 🚨 THE GREAT AIRFLOW OFFENDER: AIR SPEED Here’s the problem: air that moves too fast gets noisy. Really noisy. Like "is that a snake in the ceiling?" noisy. So how do we fix it? We follow the golden rule of studio HVAC design: Keep that air speed below 300 FPM (Feet Per Minute). And never, ever go above 500 FPM unless you want your vents to start beatboxing. 📏 STEP 1: KNOW YOUR AIRFLOW – CFM VS FPM Let’s get nerdy for a sec (don’t worry, no pop quiz). * CFM (Cubic Feet per Minute) = how much air is moving. * FPM (Feet per Minute) = how fast the air is moving. Think of it like this: * CFM is how much pizza you're delivering. * FPM is how fast you're driving the pizza to the studio. Too fast? Pizza toppings everywhere. Too loud? You ruin the take. 🧠 STEP 2: DO THE MATH (JUST ONCE, PROMISE) Let’s say your studio is 400 square feet with a 9.5-foot ceiling. That’s 3,800 cubic feet of air. Now use this formula: Room Volume × 6 Air Changes / 60 Minutes = Required CFM So, in our example: 3,800 × 6 / 60 = 380 CFM Congrats! You just earned your HVAC math badge. 🎖️ 🛠️ STEP 3: DUCTULATOR TO THE RESCUE If you’ve never heard of a Ductulator, no, it’s not a lost Marvel character. It’s a tool (free online) where you plug in your airflow (CFM) and desired air speed (FPM), and it tells you what duct size you need. Pro Tip: Set your max air velocity to 300 FPM in the calculator. Put in your CFM (e.g., 380). Boom! Now you know the duct size that keeps your air whisper-level quiet. ❄️ STEP 4: CONSIDER THE COOL KID ON THE BLOCK – DUCTLESS MINI-SPLITS You know what doesn’t make noise? Ductless mini-split systems. They’re sleek, quiet, and perfect for home studios. Plus, they don’t blow air through ducts, so no air speed drama. Pair them with an Energy Recovery Ventilator (ERV) and you’ve got both temperature control and fresh air. 👥 STEP 5: DON'T FORGET THE HUMANS Now, let’s talk ventilation. People need oxygen (shocking, we know). So if your studio gets packed with your band, their gear, and one overenthusiastic producer, you need to ventilate that air out. Use this rule: 15 CFM per person So if 10 people are in the room (maybe you're recording a choir or hosting a very cozy podcast), that’s 150 CFM just for ventilation. 😱 DANGER ZONE: NEGATIVE PRESSURE If your system only supplies air but doesn’t return it, you create negative pressure. Translation: your studio becomes a vacuum cleaner trying to suck in sound from the rest of the house. Solution: Always design both supply and return ducts. Balance is everything (ask any audio engineer or Jedi). 💡 FINAL THOUGHTS FROM THE (SOUNDPROOF) TRENCHES Designing HVAC for a home studio is a lot like mixing a great song—it’s all about balance and detail. The right air speed makes sure your HVAC system doesn’t become an unexpected backup vocalist. So remember: * Keep air speed under 300 FPM * Use a ductulator to size your ducts * Go ductless if you can * And don’t forget to ventilate for actual humans Need help making all this real for your studio? 👉 Book a Soundproof Clarity Call [https://www.soundproofyourstudio.com/Step1%20] Or jump into our Free Soundproofing Workshop [https://www.soundproofyourstudio.com/workshop] to learn more about designing quiet, high-performance studios. P.S. If your HVAC sounds like Darth Vader during your takes... it’s time to revisit your duct design. Your ears (and clients) will thank you.
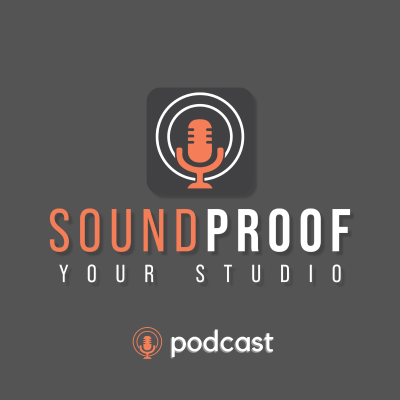
🎧 CAN YOU PARTIALLY SOUNDPROOF A ROOM? HERE'S THE TRUTH (FROM A PRO) Let’s cut to the chase, you want a quieter space. Maybe it's to stop the drum kit from rattling your walls or to keep noisy neighbors out of your creative zone. Naturally, your first question is: “Can I just soundproof one wall?” or “Can I get by with soundproofing only the ceiling?” Spoiler alert: You can try. But it won’t work the way you’re hoping. 🚫 THE MYTH OF PARTIAL SOUNDPROOFING We hear it all the time: "I just want to soundproof the door." "I’ll handle the ceiling now, then the rest later." But here's the truth: Soundproofing is not like painting one wall a different color. It's not something you can piecemeal and expect real results. WHY? Because sound travels in all directions, through walls, floors, ceilings, even ventilation and electrical gaps. Blocking just one path is like trying to stop a leak with a napkin. 🔍 SO WHAT ACTUALLY WORKS? ✅ THE HOLISTIC APPROACH Effective soundproofing means thinking about the entire room as a system. That includes: * All four walls * The ceiling and floor * Doors and windows * And yes, even HVAC systems You need to isolate every path that sound can use to sneak in or out. That’s the only way to create a truly sound-isolated space. 💸 WHAT ABOUT BUDGET? Let’s be real, full soundproofing isn’t cheap. You might need to: * Take walls down to the studs * Build a floating floor or add mass-loaded vinyl * Isolate HVAC ducts * Use soundproof doors and acoustic sealant It’s an investment, but it’s also the only way to get professional-level results. If you try to save now with a half-done job, you'll likely end up spending more later to fix what didn’t work. 🧠 SOUND SCIENCE, NOT SOUNDPROOFING SCAMS Some folks online will sell you “soundproof” panels or stick-on foam with big promises. But real sound isolation is based on physics: * Mass (heavier materials block sound) * Decoupling (separating surfaces prevents vibration transfer) * Air gaps and insulation (reduce sound bridges) Foam helps with echo control — not soundproofing. 👀 STILL NOT SURE WHERE TO START? That’s totally normal! Most people don’t know this stuff until they go down the rabbit hole or waste money on the wrong materials. But here’s the good news: 🎓 YOU CAN JOIN OUR FREE SOUNDPROOFING WORKSHOP [https://www.soundproofyourstudio.com/workshop] AND LEARN THE REAL DEAL. We’ll walk you through the fundamentals and help you avoid expensive mistakes. Or if you're more of a 1-on-1 learner, book a free clarity call [https://www.soundproofyourstudio.com/Step1] with me. We’ll talk about your space, your goals, and what makes the most sense for your budget. YOU CAN'T CHEAT SOUNDPROOFING If you’re asking “Can I partially soundproof my room?” — the answer is: You can, but it won’t work well. If you want real isolation, go all in or at least plan for a full-room solution over time. 🎤 Questions? Jump into the workshop or let’s talk on a free clarity call. Your ears (and your neighbors) will thank you.
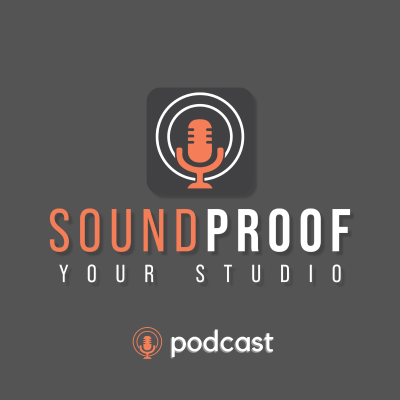
What You Need to Know Before Soundproofing a Room If you're planning to soundproof a room, especially in an older garage, basement, or converted space, there’s one question you absolutely must ask: Can your ceiling hold the weight? Soundproofing materials are heavy. Before you start layering mass-loaded vinyl, double drywall, or other dense products, you need to make sure your ceiling structure can safely support the load. Here’s how. STEP 1: ASSESS YOUR EXISTING CEILING STRUCTURE Before you add anything, take a good look at what you already have: * What kind of space is this? (Garage, attic, bonus room?) * What was the ceiling originally designed to support? * Are there visible beams or joists? Measure the spacing between them. Many older ceilings, especially in garages built in the 1950s or 60s, were not designed to hold significant weight beyond drywall and light fixtures. STEP 2: UNDERSTAND WEIGHT LIMITS Most residential ceiling structures can only support a limited load, often just ½” drywall and basic insulation. When soundproofing, even without products like MLV, you're still adding significant weight with: * Two layers of ⅝” drywall * Resilient channels or sound isolation clips * Possible additional framing or mass layers These materials add up quickly in terms of weight per square foot. You need to calculate the total added load and compare it to what your existing ceiling can safely handle. STEP 4: CONSIDER SMART DESIGN ALTERNATIVES If you're tight on ceiling height or structure isn’t ideal, consider: * Using pre-engineered scissor trusses * Designing a room-within-a-room that floats below the ceiling joists * Consider using pre-engineered beams for cathedral ceiling These methods help preserve structural integrity while still achieving excellent sound isolation. STEP 5: REVIEW AND ADJUST BEFORE YOU BUILD Before construction begins: * Review your engineer’s drawings * Walk through the plan with your contractor * Make final design changes to avoid costly mistakes And remember, never install heavy ceiling layers based on guesswork. KEY CAUTIONARY NOTES * Don’t underestimate weight. More mass means more stress on your ceiling. * Don’t skip the engineer. It’s not just about code, it's about safety. * Don’t rely solely on your builder. Soundproofing introduces unique structural demands. BONUS: TIPS FOR STAYING ON TRACK * Use design software to visualize your framing and ceiling layout. * Document all assessments and engineer recommendations. * Communicate clearly with your builder and team at each stage. READY TO START YOUR PROJECT? Soundproofing a space is a big investment, and structural mistakes can be costly. If you want expert help assessing your space and getting a customized plan: 👉 Book a free Soundproof Clarity Call [https://www.soundproofyourstudio.com/Step1] 👉 Join our Free Soundproofing Workshop [https://www.soundproofyourstudio.com/workshop] We’ll help you build a quiet space—without risking a ceiling collapse.
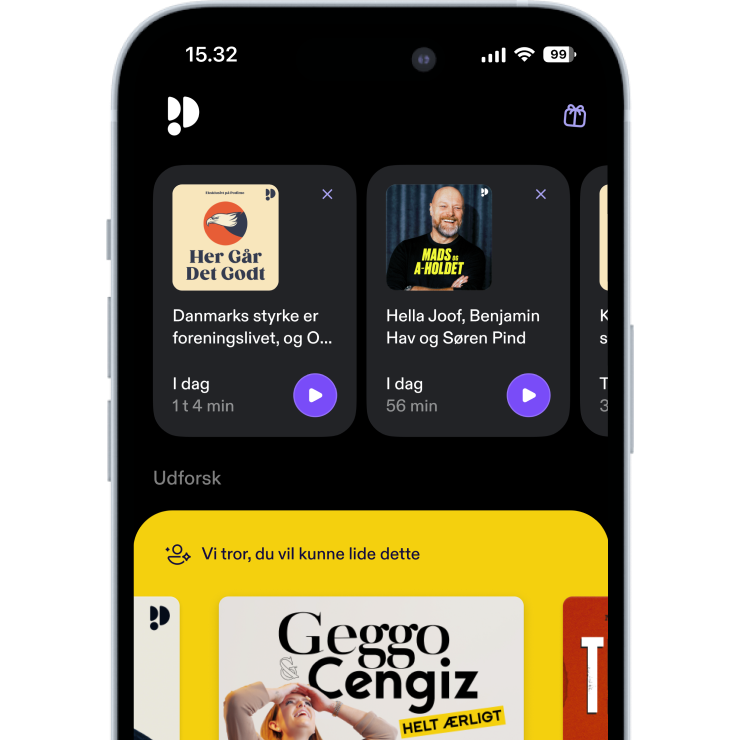
Rated 4.7 in the App Store
Prøv gratis i 7 dage
99 kr. / måned efter prøveperiode.Ingen binding.
Eksklusive podcasts
Uden reklamer
Gratis podcasts
Lydbøger
20 timer / måned